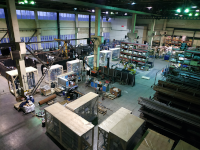
Монтаж инженерных коммуникаций, в том числе систем тепло- и холодо- и водоснабжения – один из наиболее сложных этапов капитального строительства. Как показывает практика, до завершения работ «доживает» менее 50 % подрядчиков. За этими цифрами – целый комплекс проблем, обусловленных как ошибками в планировании, так и низким качеством проектирования и монтажа инженерных систем.
Часто можно видеть, как проект теплового пункта или холодильного центра выполняет одна компания, начинает его монтаж другая, а заканчивает третья. Порой эта цепочка еще длиннее. Результат – срыв сроков сдачи объекта, работа «в ноль» или «в минус», хозяйственные споры с заказчиком и масса проблем при последующей эксплуатации. Может показаться, что от самих подрядчиков здесь зависит немногое, ведь они являются заложниками ситуации и мало на что могут повлиять. Однако опыт компании «ОМП-Инжиниринг» показывает, что разорвать порочный круг можно, но для этого нужно полностью переосмыслить подходы к проектированию и монтажу.
Факторы риска при организации работ
Проблемы, которые ведут к срыву сроков и снижению рентабельности подрядных работ, возникают не одномоментно: они накапливаются в течение всего периода реализации проекта. В их числе следует выделить наиболее существенные:
- Низкое качество проектирования и рабочей документации. Прежде всего, это отсутствие монтажного проекта. Нередко проектирование производится без должного учета особенностей конфигурации здания и его помещений, удобства монтажа и последующей эксплуатации оборудования. Точность позиционирования элементов системы также часто оставляет желать лучшего, а 3D-модель если и присутствует, то является схематичной. Зачастую проект и отдельные элементы системы приходится «подгонять» уже по месту, причем делает это прораб монтажной бригады. В результате сроки монтажа увеличиваются, а его качество снижается.
- Задержки предоставления строительной готовности под монтаж. При традиционном подходе к организации работ подрядчик не может повлиять на этот фактор и вынужден ждать. Ожидание часто сопряжено с простоем оборудования и персонала, что ведет к росту производственных затрат. При этом, несмотря на простои по вине смежников, заказчик нередко требует завершить монтаж вовремя. Например, если необходимо сдать объект к определенной дате (чемпионат по футболу, визит официального лица, начало учебного года и т.п.) или к началу отопительного сезона.
- Задержка поставок оборудования (насосы, теплообменники и пр.), в том числе в результате финансовых трудностей у заказчика. В подобной ситуации монтажные работы могут быть приостановлены на неопределенный срок с теми же последствиями, что и в случае задержки стройготовности.
- Низкое качество планирования сроков производства монтажных работ, отсутствие нормирования.
- Нехватка квалифицированного персонала. Особенно критичным этот фактор становится на завершающем этапе, когда возникает необходимость в корректировках проекта и сокращении сроков монтажа.
Сумма перечисленных проблем становится причиной резкого увеличения трудоемкости проекта на завершающем этапе его реализации. На площадке возникают «авралы», которые либо ведут к срыву установленных сроков, либо преодолеваются путем различных нарушений технологии и регламентов производства работ, в ущерб их качеству.
Современный подход к проектированию
Качество проектирования – необходимое условие успешной и своевременной реализации проекта. Здесь хороший пример подают европейские компании, которые зачастую тратят на проработку проекта и рабочей документации куда больше времени, чем на строительство.
➢ Алексей Панафидин, исполнительный директор «ОМП-Инжиниринг»:
В своей практике мы пересмотрели организацию проектных работ, отказались от применения традиционных для отечественных проектировщиков программных средств и перешли к конструированию гидравлических узлов с использованием системы машиностроительного проектирования SOLID WORKS. При этом мы принимаем в расчет не только технические требования к системе, но и особенности ее пространственной 3D-компоновки для обеспечения эффективности, удобства монтажа и эксплуатации в условиях конкретного объекта.
Такой подход не просто обеспечивает значительно более высокую степень детализации и точности (до 2,5 мм на 1000 мм линейного размера), но и позволяет получить из 3D-модели чертежи отдельных деталей и узлов, которые необходимы для их производства в заводских условиях. Кроме того, рабочая документация в обязательном порядке содержит сборочные схемы и монтажный проект, включающий все необходимые металлоконструкции, опоры, монтажные инструкции и пр. и обеспечивающий 100 % собираемость системы на объекте.
Оптимизация монтажных процессов
Высокое качество проектирования и проработки рабочей документации позволяет не просто сократить время и повысить качество монтажа, но и перенести значительную часть операций с объекта в производственный цех. Благодаря этому сегодня большую часть сборочно-сварочных операций (в частности, трубное производство и практически весь объем сварочных работ в диапазоне диаметров до 600 мм) «ОМП-Инжиниринг» выполняет не на стройплощадке, а на собственной производственной площадке.
➢ Алексей Панафидин:
«Фактически монтажные работы начинаются сразу после утверждения проектной документации, независимо от того, на какой стадии строительства находится сам объект. В период ожидания поставок оборудования и стройготовности площадки выработка трудоемкости по проекту начинается в цеховых условиях. За счет распараллеливания процессов риски нарушения сроков реализации проекта существенно снижаются».
Сейчас на производстве компании в подмосковной Ивантеевке используются промышленное оборудование ведущих мировых производителей: системы плазменной резки труб, сварочное оборудование и монтажные столы, трубогибочные станки, покрасочно-сушильные камеры и пр. На очереди – роботизация сварочного производства. Есть и собственные разработки, например, универсальная оснастка и фланцевы кондукторы, которые позволяют унифицировать все процессы технологического цикла компании. Благодаря этому изготовление любых элементов сводится к стандартизированному набору операций, выполняемых в соответствии с технологической картой и нормированных по времени. Такой подход позволяет гарантировать высокое качество отдельных узлов, собираемость конструкции и своевременное завершение работ.
Готовые элементы трубопроводов и сварные соединения проходят ВИК-контроль (его осуществляют аттестованные НАКС технологи) и промежуточные гидравлические испытания на опрессовочном стенде собственной разработки компании. Еще раз холодильный центр или тепловой узел, как и положено, будет опрессован уже в сборе, на объекте. Кроме того, производится выборочный УЗК- либо рентген-контроль отдельных узлов в аттестованной лаборатории.
➢ Алексей Панафидин:
”На сегодняшний день степень заводской готовности наших решений составляет 60-80 %. После завершения роботизации сварочных операций этот показатель станет еще выше. На объекте остается выполнить минимум работ, фактически – собрать по инструкции конструктор из готовых элементов. Отсутствие сложного монтажа и сварки позволяют сделать это за минимальное время и без привлечения высококвалифицированного персонала. Поэтому проблемы сроков у нас нет. Даже если поставки элементов системы от других производителей задерживаются, благодаря высокой точности производства мы можем использовать вместо них временные макеты и не допускаем простоев».
Эффективность и контроль
Как показала практика, помимо технологических преимуществ оптимизация монтажных процессов приносит и экономическую выгоду ввиду существенного снижения уровня рисков.
При этом заказчик имеет возможность контролировать процесс с момента начала проектирования. Действующая на предприятии система оперативно-календарного планирования на базе облачного решения Fieldwire протоколирует результаты работы на каждом этапе производства и позволяет дистанционно контролировать реализацию проекта, вносить замечания и устранять недочеты в режиме реального времени.
В условиях кризиса строительной отрасли и растущего дефицита оборотных средств оптимизация монтажных процессов становится одним из факторов снижения рисков при одновременном повышении качества и сокращении сроков выполнения монтажных работ.
➢ Справка о компании:
”ОМП-Инжиниринг» – российская компания, специализирующаяся в области проектирования, производства и монтажа тепловых пунктов, холодильных центров и насосных станций высокой степени заводской готовности. В числе реализованных проектов – Политехнический музей, Центр художественной гимнастики Ирины Винер‑Усмановой и Ледовый дворец «Кристалл» в Лужниках, ВТБ Арена стадион «ДИНАМО», московский стадион ЦСКА, ЖК «Лайнер» на Ходынке, Radisson Blu Olympiyskiy Hotel Moscow, Отель DoubleTree by Hilton Moscow – Marina и др.